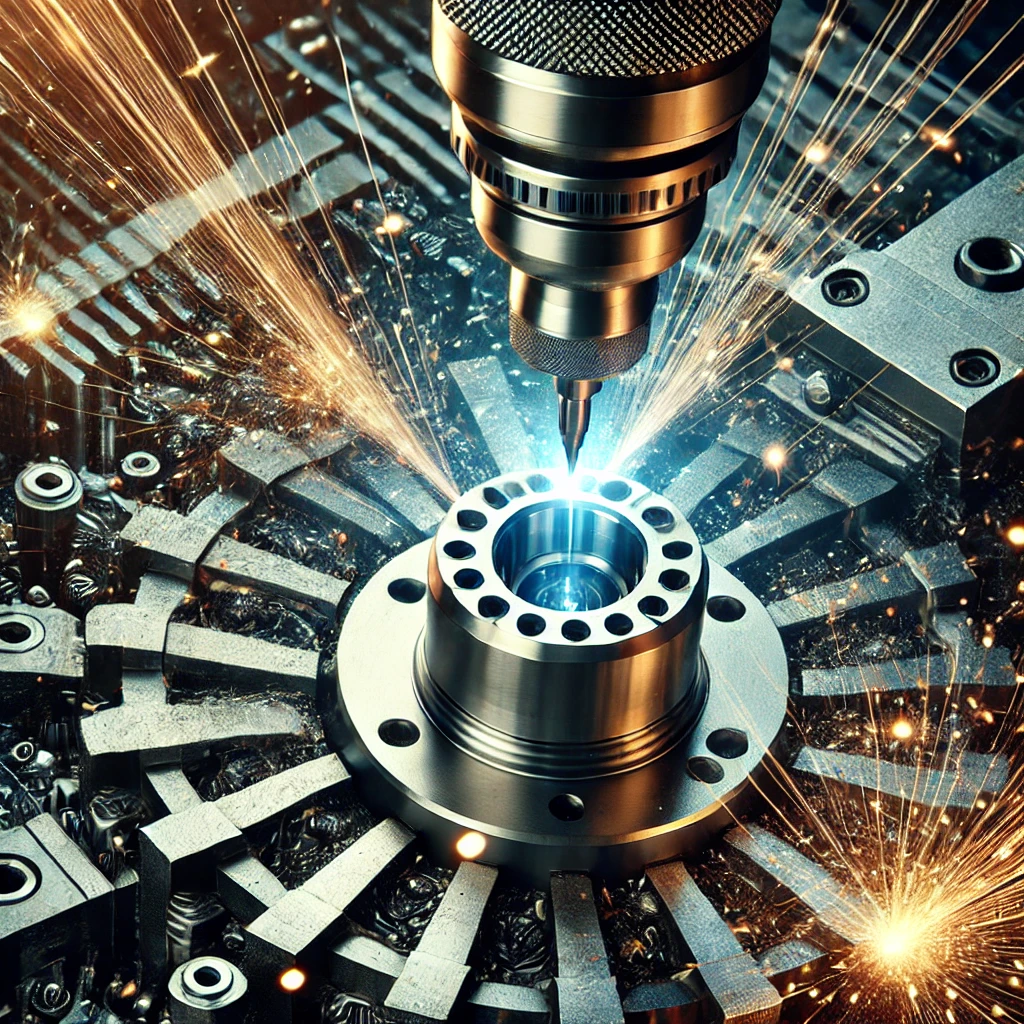
目次
放電加工とは?
放電加工(EDM)は、電気エネルギーを利用して金属を加工する高度な技術です。簡単に言うと、電極と被加工物の間に放電を発生させ、その電気の力で金属を溶かしながら形を整える方法です。これによって、従来の切削加工では難しい非常に硬い金属や複雑な形状の加工が可能になります。
放電加工の仕組み
放電加工の基本的な仕組みは次の通りです:
- 加工液の供給: 工具電極と被加工物の間に絶縁性の加工液(一般的には油や水)を流します。この加工液は、電気の流れを制御し、放電が発生するのを助ける役割を果たします。
- 放電の発生: 工具電極と被加工物の間に高周波の電気を流し、短時間で高温の放電を発生させます。この放電によって、金属の微小な部分が一瞬で溶けて蒸発します。
- 金属の溶解: 放電によって発生する熱で金属を溶かし、形を整えます。溶けた金属は、加工液によって冷却され、加工液の中に流れ出します。
- 冷却と洗浄: 加工液は、溶けた金属の微粒子を洗い流し、電極と被加工物の間を冷却します。
放電加工に適した素材
放電加工は、電気を通す素材であればほとんどの金属に適用できます。以下は代表的な素材です:
- 鉄: 一般的な金属で、多くの産業で使用されます。
- ステンレス: 耐食性が高く、医療機器や食品産業で使用されます。
- アルミニウム: 軽量であり、航空機や自動車部品に利用されます。
- チタン: 高強度かつ軽量であり、航空宇宙や医療分野で使用されます。
- ニッケル合金: 高温に強く、ガスタービンやエンジン部品に使用されます。
放電加工の主な種類
放電加工には、主に以下の2つの種類があります。それぞれの特徴と用途について説明します。
ワイヤー放電加工
ワイヤー放電加工(Wire EDM)は、細いワイヤーを電極として使用し、被加工物を切断する方法です。非常に細かい切断が可能で、複雑な形状の加工に適しています。
- 用途: 金型製作、精密部品の切断
- 特徴: 高精度で複雑な形状の加工が可能
形彫放電加工
形彫放電加工(Sinker EDM)は、特定の形状を持つ電極を使用し、その形を被加工物に転写する方法です。主に型彫りや金型の製作に使用されます。
- 用途: 金型、ダイの製作
- 特徴: 任意の形状を精密に彫刻可能
放電加工を施すメリット・デメリット
放電加工には多くの利点といくつかの欠点があります。
- 高精度な加工が可能: 非常に細かい部分まで加工できます。
- 硬度の高い素材も加工可能: 超硬合金などの硬い金属も簡単に加工できます。
- 熱影響が少ない: 加工時の熱変形が少ないため、高精度な仕上がりが得られます。
- 複雑な形状が作れる: 切削加工では不可能な複雑な形状の加工が可能です。
- 加工速度が遅い: 切削加工に比べて時間がかかります。
- 電極の消耗: 電極が消耗するため、定期的な交換が必要です。
- 高コスト: 設備や運用コストが高いです。
- 限定された材料: 導電性のない材料は加工できません。
放電加工と電解加工との違い
放電加工と電解加工(Electrochemical Machining, ECM)は、どちらも電気を利用した加工方法ですが、原理が異なります。
- 放電加工: 放電による熱で金属を溶かします。非接触で高精度な加工が可能です。
- 電解加工: 電気化学反応を利用して金属を溶かします。こちらは化学反応による溶解なので、工具の消耗が少ないです。
放電加工 vs. 電解加工
特徴 | 放電加工 | 電解加工 |
---|---|---|
原理 | 放電による熱で溶解 | 電気化学反応で溶解 |
精度 | 高い | 高い |
工具の消耗 | あり | 少ない |
適用素材 | 導電性のある金属 | 導電性のある金属 |
まとめ
放電加工は、硬度の高い金属や複雑な形状の加工に最適な技術です。特に高精度な加工が求められる場合に有効ですが、加工速度の遅さや高コストがデメリットとなります。電解加工との違いを理解し、適材適所で使い分けることが重要です。
Point: 放電加工は、電気を利用して金属を加工する技術で、高精度な加工が可能です。しかし、加工速度が遅く、コストが高い点に注意が必要です。電解加工との違いも理解して使い分けましょう。
ワイヤーカットとは?その仕組みと用途、メリット・デメリット
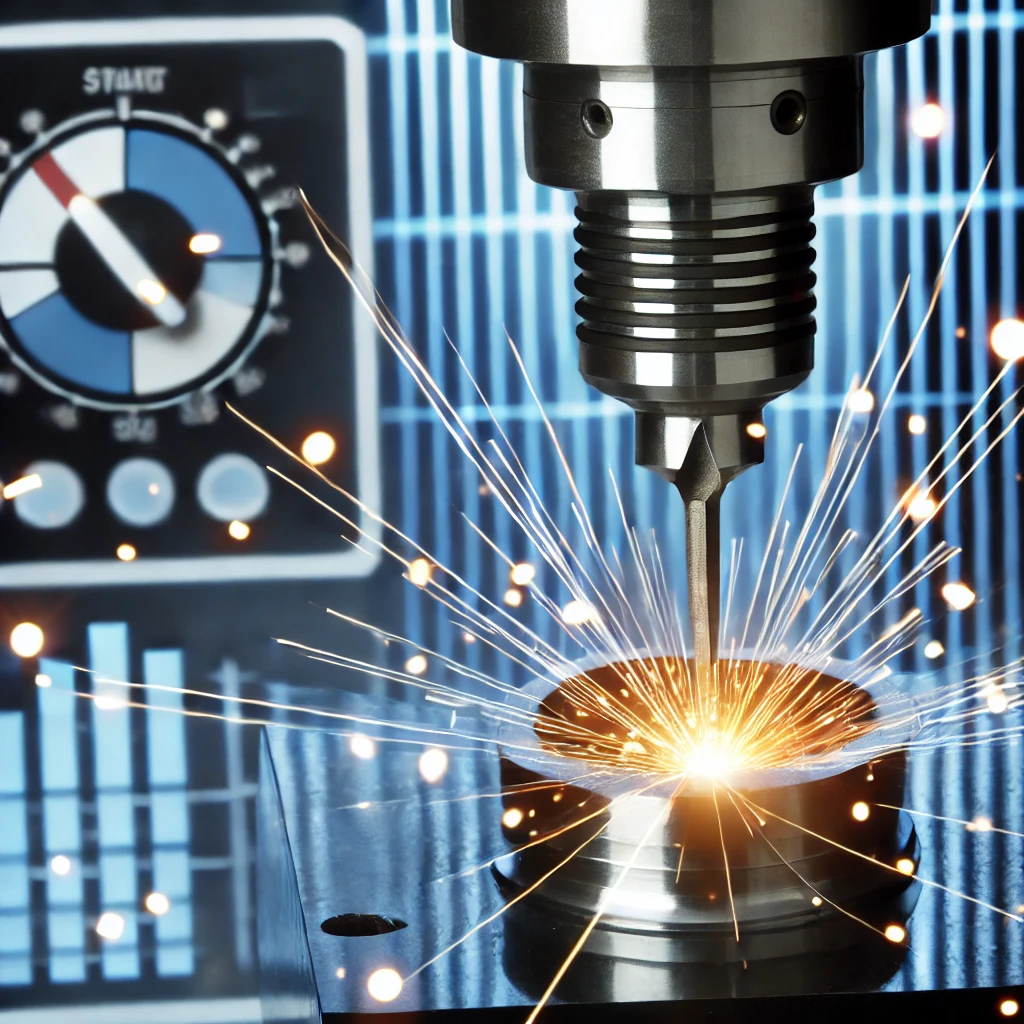
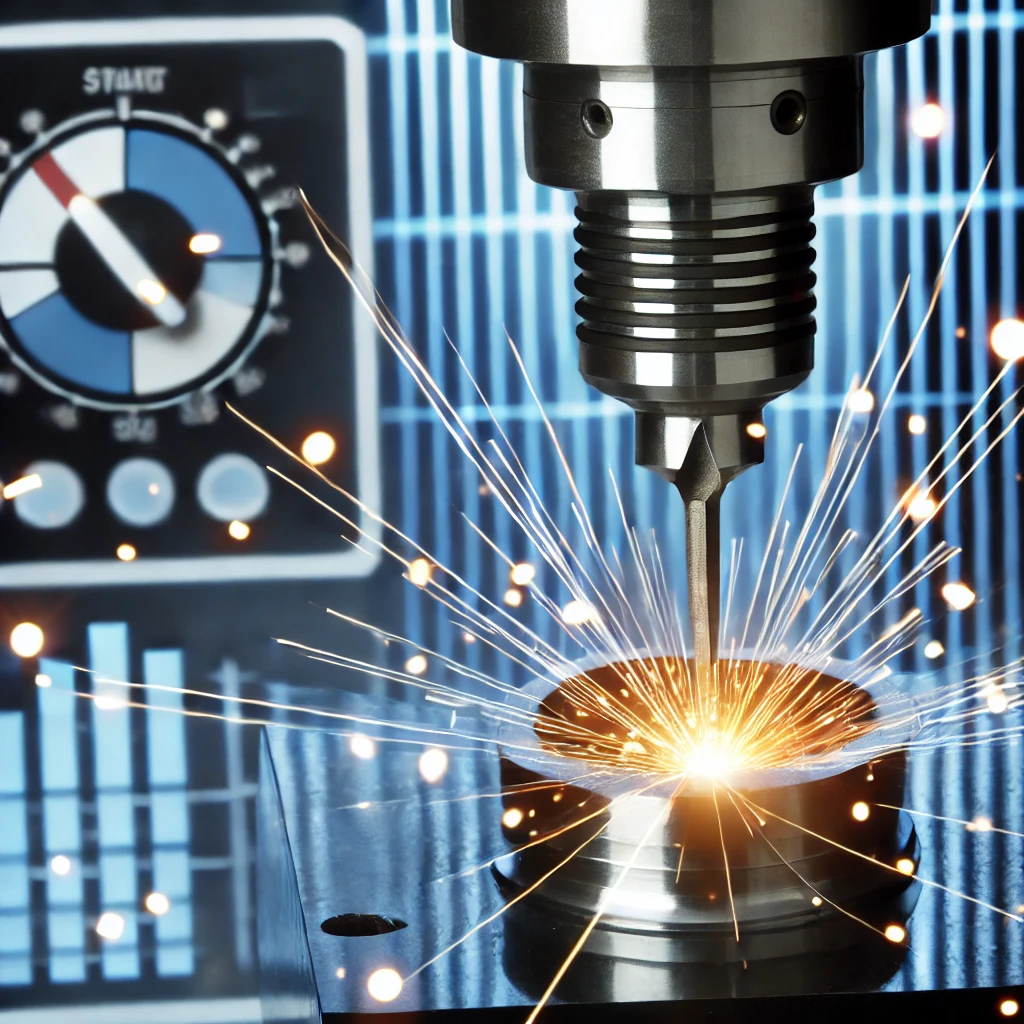
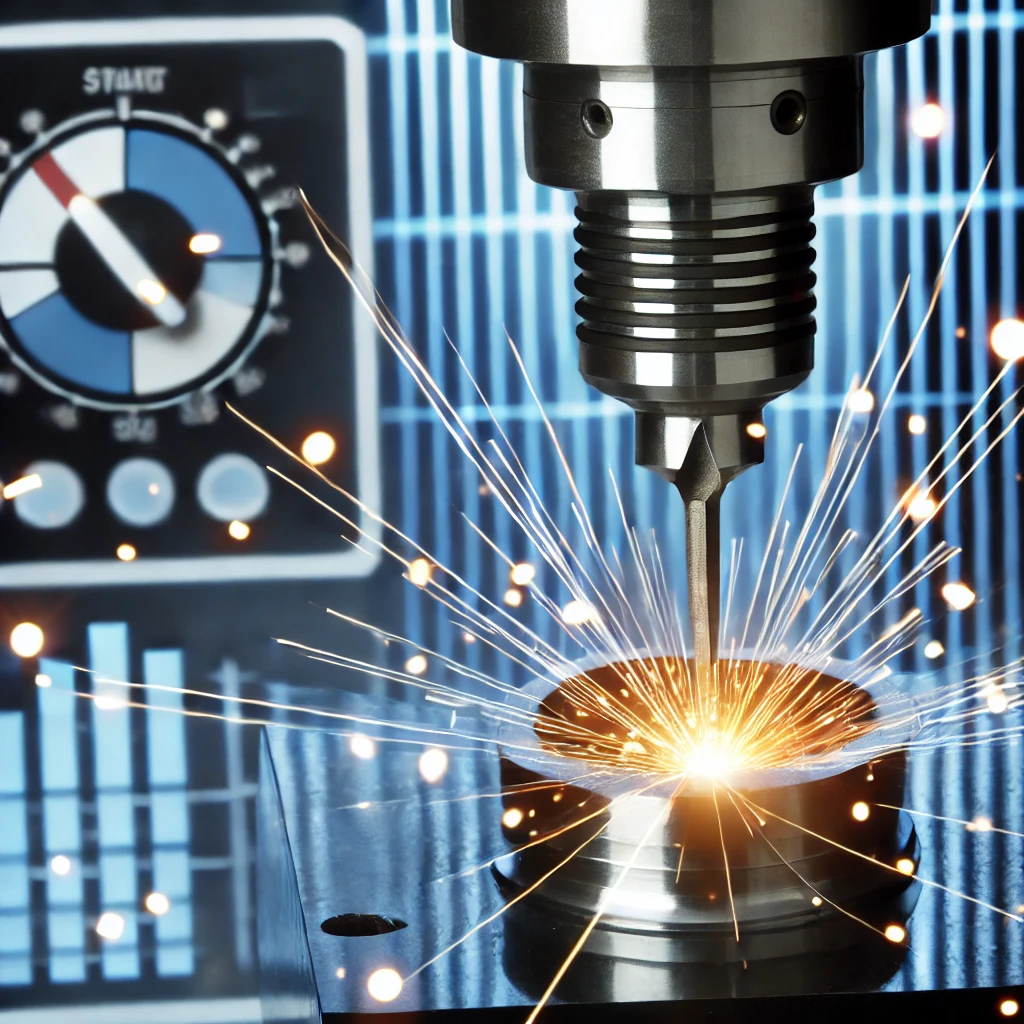
ワイヤーカットとは?
ワイヤーカットは、細いワイヤーを電極として使用し、金属を切断する放電加工の一種です。ワイヤーに高周波の電気を流し、その放電によって金属を溶かして切断します。非常に細かい切断が可能で、複雑な形状の加工に適しています。
ワイヤーカットの仕組み
ワイヤーカットの基本的な仕組みは次の通りです:
- ワイヤーの供給: 細い金属ワイヤーを電極として使用します。ワイヤーは連続的に供給され、加工中に消耗しても新しい部分が使用されます。
- 放電の発生: ワイヤーと被加工物の間に高周波の電気を流し、放電を発生させます。これにより、金属が一瞬で溶けて蒸発します。
- 金属の溶解: 放電によって発生する熱で金属を溶かし、切断します。
- 冷却と洗浄: 加工液で溶けた金属を冷却・洗浄し、加工の精度を保ちます。
ワイヤーカットの用途
ワイヤーカットは、その高精度な切断能力から、以下のような用途に広く使用されています:
- 金型製作: 精密な金型の製作に適しています。
- 精密部品の切断: 微細な部品の切断や製作に利用されます。
- 医療機器の製造: 高い精度が求められる医療機器の製造に使用されます。
- 航空宇宙部品の製作: 高強度かつ軽量な部品の製作に最適です。
ワイヤーカットのメリット・デメリット
- 高精度な切断が可能: 非常に細かい部分まで切断できます。
- 複雑な形状の加工が可能: 曲線や複雑なデザインの加工に最適です。
- 熱影響が少ない: 加工時の熱変形が少ないため、精密な仕上がりが得られます。
- 表面品質が高い: 切断面が滑らかで、後処理が少なくて済みます。
- 加工速度が遅い: 大量生産には不向きです。
- 消耗品のコスト: ワイヤーの消耗が早いため、定期的な交換が必要です。
- 高コスト: 設備や運用コストが高いです。
ワイヤーカットの種類
ワイヤーカットにはいくつかの種類があり、それぞれの特徴があります。
- 直線ワイヤーカット: 主に直線の切断に使用されます。簡単な形状や直線的な部品の加工に適しています。
- 曲線ワイヤーカット: 複雑な曲線や形状の切断に使用されます。デザイン性の高い部品や複雑な構造の加工に最適です。
ワイヤーカットの使用上の注意点
ワイヤーカットを使用する際には、以下の点に注意が必要です:
- 適切なワイヤー選び: 加工する素材に適したワイヤーを選ぶことが重要です。ワイヤーの材質や直径は、加工精度に大きな影響を与えます。
- 安全対策: 高電圧を使用するため、適切な安全対策が必要です。加工中の放電により、火花や高熱が発生するため、適切な防護策を講じましょう。
- 定期的なメンテナンス: ワイヤーや加工液の定期的な交換とメンテナンスが必要です。これにより、加工精度の維持と機械の長寿命化が期待できます。
まとめ
ワイヤーカットは、高精度で複雑な形状の切断が可能な加工方法です。特に精密部品や金型製作に適しており、熱影響が少ないため、高精度な仕上がりが求められる場合に有効です。しかし、加工速度の遅さやコストの高さがデメリットとなります。
Point: ワイヤーカットは、細いワイヤーを使用して高精度な切断を行う技術です。複雑な形状の加工に最適ですが、加工速度が遅く、消耗品のコストがかかる点に注意が必要です。
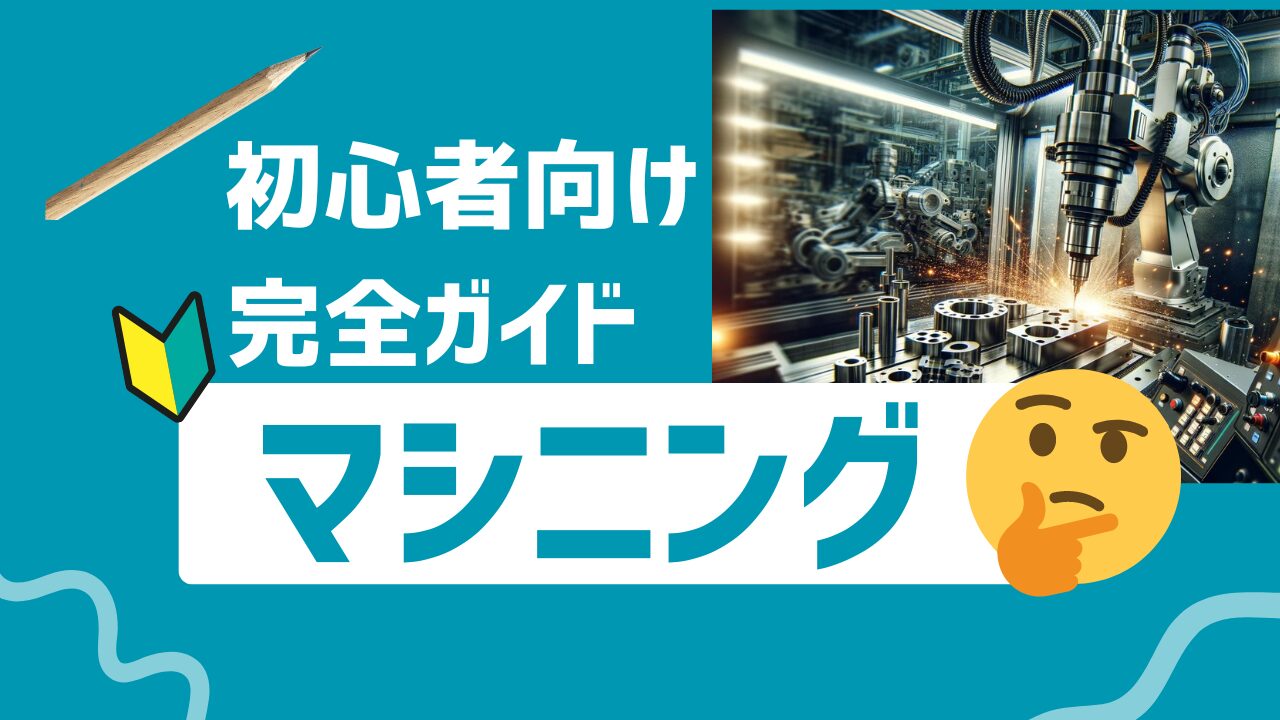
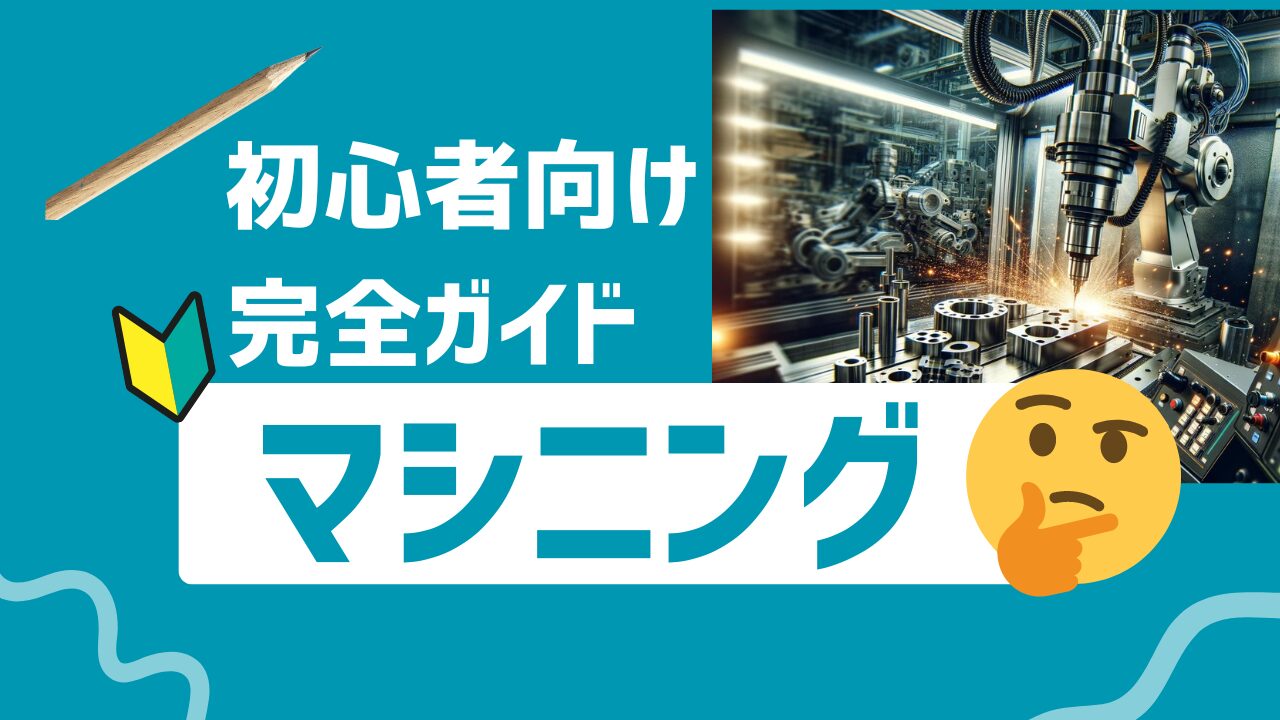
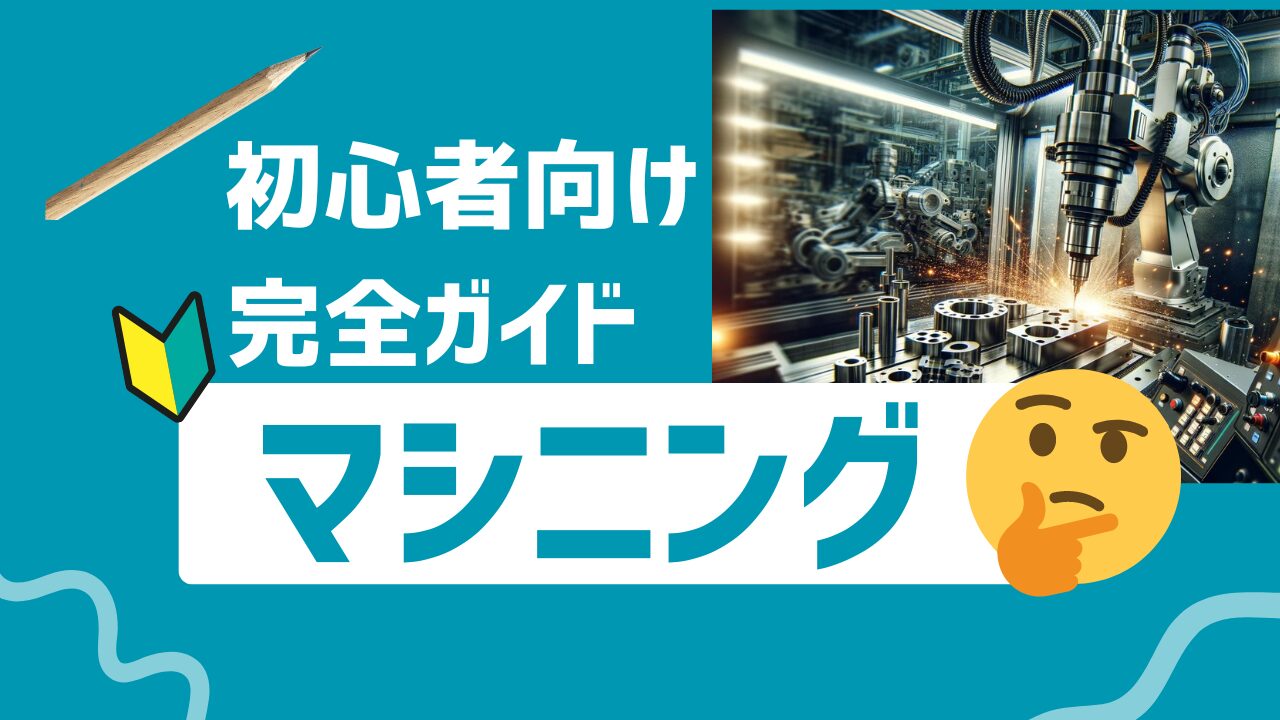