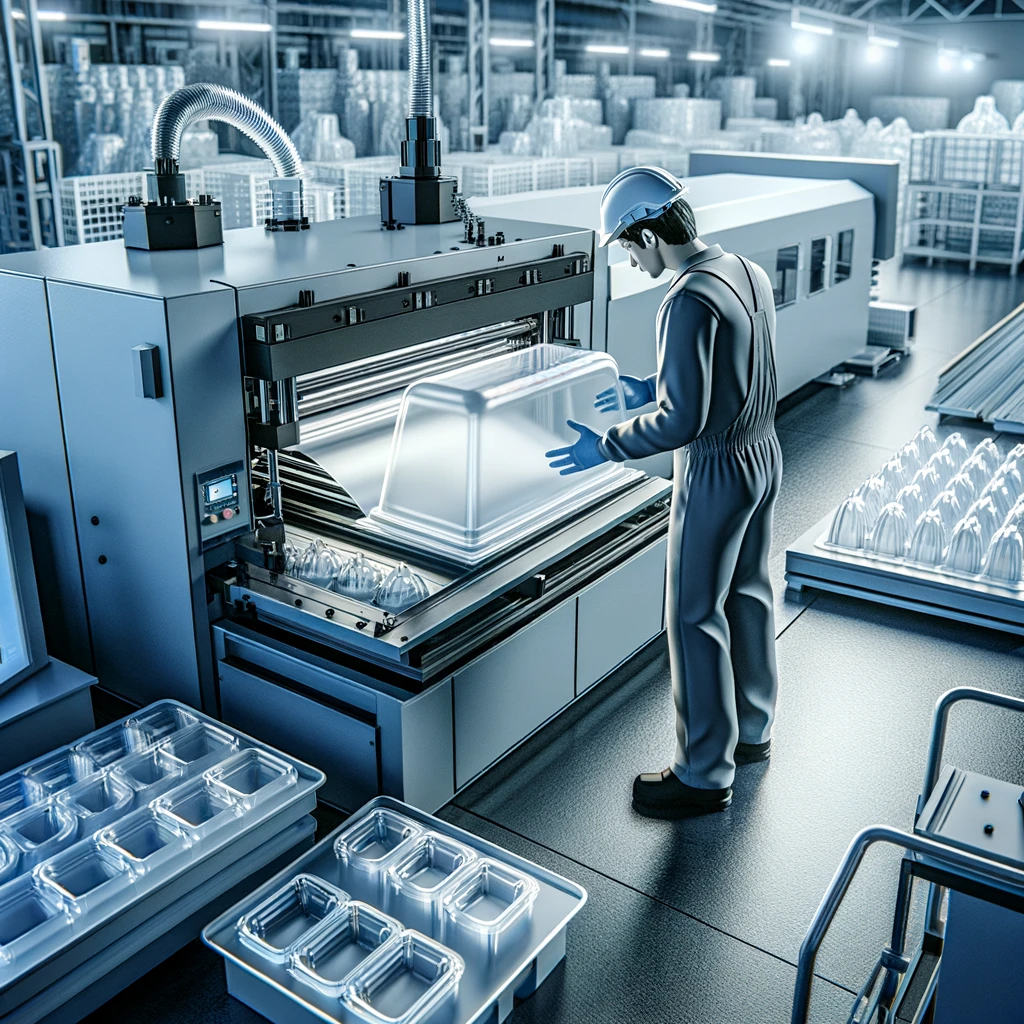
目次
真空成形と圧空成形の基本知識
真空成形の概要
真空成形は、熱可塑性プラスチックシートを加熱して柔らかくし、真空を利用して金型に密着させて成形する技術です。対応できるサイズも様々で量産まで対応も可能です。
真空成形とは?
真空成形は、加熱したプラスチックシートを真空ポンプで金型に吸引して成形する工法です。薄いシートを使うことが多く、大型のカバーやパネルなどに利用されます。例えば、家電製品の外装や自動車のパネル、さらには医療機器のケースなど、多岐にわたる用途があります。
真空成形のメカニズム
真空成形のメカニズムは以下の通りです。これらの工程を経て製品が作られます。
- シートの加熱:プラスチックシートをオーブンなどで加熱して柔らかくします。
- 真空吸引:加熱したシートを金型の上に置き、真空ポンプで空気を吸引してシートを金型に密着させます。
- 冷却:シートが金型に密着した状態で冷却され、形が固定されます。
- トリミング:不要な部分を切り取って仕上げます。
真空成形のメリットとデメリット
メリット:
- 大型の成形品が低コストで製作可能
- 型の作製費が安い
- 短納期での生産が可能
- プロトタイプから量産まで対応できる
デメリット:
- 細かなディテールが再現しにくい
- 厚みや寸法にばらつきが出やすい
- 一部の材料では成形が難しい場合がある
真空成形の型について
真空成形で使用される型には、木型、樹脂型、金属型があります。それぞれの特徴は以下の通りです。
- 木型:コストが低く、プロトタイプや小ロット生産に適していますが、耐久性に欠けます。
- 樹脂型:中程度のコストで、中ロットの生産に適しています。耐久性は木型よりも高いです。
- 金型:高コストですが、耐久性が非常に高く、大ロットの生産に適しています。
真空成形に使用される主な樹脂素材
真空成形に使用される主な樹脂素材には以下のものがあります。
- ABS:強度と耐衝撃性に優れ、家電製品や自動車部品に使用されます。
- PVC:耐薬品性があり、医療機器や化学装置に使用されます。
- PET:透明性が高く、食品包装や飲料容器に使用されます。
- PC:耐熱性と耐衝撃性に優れ、電子機器や防護具に使用されます。
圧空成形の概要
圧空成形は、真空成形の応用技術で、金型にプラスチックシートを押し付ける圧力を加えることで、より高精度な成形が可能です。
圧空成形とは?
圧空成形は、熱可塑性プラスチックシートを加熱し、真空と空気圧を使って金型に押し付けて成形する方法です。この方法は、真空成形に比べて複雑な形状や細かなディテールの再現が可能です。
圧空成形のメカニズム
圧空成形のメカニズムは以下の通りです。
- シートの加熱:プラスチックシートを加熱して柔らかくします。
- 真空吸引と空気圧加圧:加熱したシートを金型に置き、真空でシートを引き寄せた後、追加の空気圧をかけてシートを金型に密着させます。
- 冷却:シートが金型に密着した状態で冷却され、形が固定されます。
- トリミング:不要な部分を切り取って仕上げます。
圧空成形のメリットとデメリット
メリット:
- 高精度でシャープな成形が可能
- 複雑な形状にも対応
- 細部のディテールが再現しやすい
デメリット:
- 真空成形に比べてコストが高くなることがある
- 加工時間がやや長い
圧空成形に使用される主な樹脂材料
圧空成形に使用される主な樹脂材料には以下のものがあります。
- ABS:強度と耐衝撃性に優れ、家電製品や自動車部品に使用されます。
- PVC:耐薬品性があり、医療機器や化学装置に使用されます。
- PETG:透明性と耐衝撃性が高く、医療機器や食品包装に使用されます。
- HIPS:高衝撃ポリスチレンで、耐衝撃性が高く、家電製品や玩具に使用されます。
Point :真空成形と圧空成形は、どちらも熱可塑性プラスチックを使用した成形方法ですが、圧空成形は追加の圧力を加えることでより高精度な製品が可能です。各成形法のメリットとデメリットを理解し、用途に応じた選択が重要です。
真空成形と圧空成形の比較
成形方法の比較
真空成形と圧空成形の違い
真空成形は真空の力のみで成形するのに対し、圧空成形は追加の空気圧を利用するため、より細かなディテールの再現が可能です。例えば、真空成形は大型のパネルやカバーに適していますが、圧空成形は複雑なデザインのディスプレイ部品や精密機器の外装に適しています。
真空成形と他工法の比較
真空成形と圧空成形は、射出成形やプレス成形と比較して初期投資が低く、大型製品の試作や小ロット生産に適しています。以下はそれぞれの工法の比較です。
- 射出成形: 高精度な成形が可能ですが、初期投資が高く、大量生産に向いています。
- プレス成形: 薄い部品の大量生産に適していますが、複雑な形状の成形には不向きです。
成形品の特徴と用途
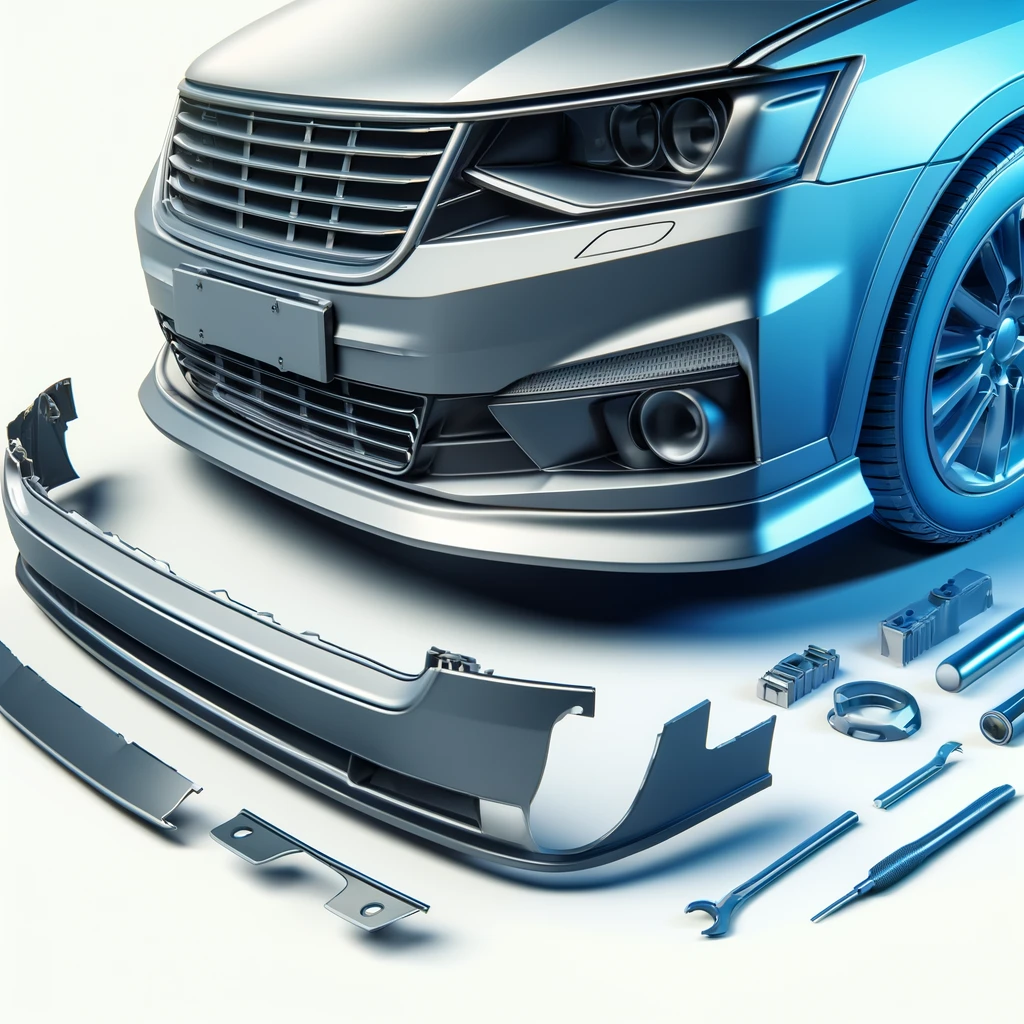
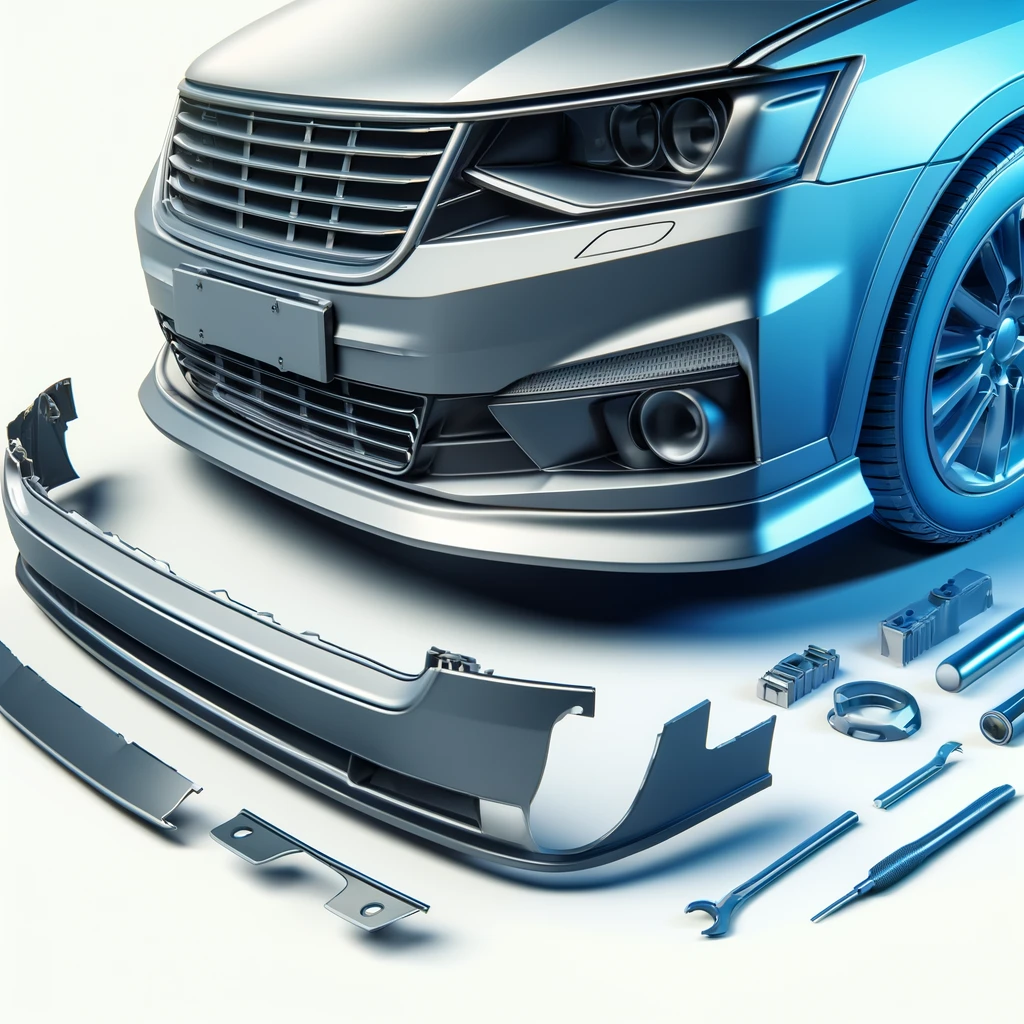
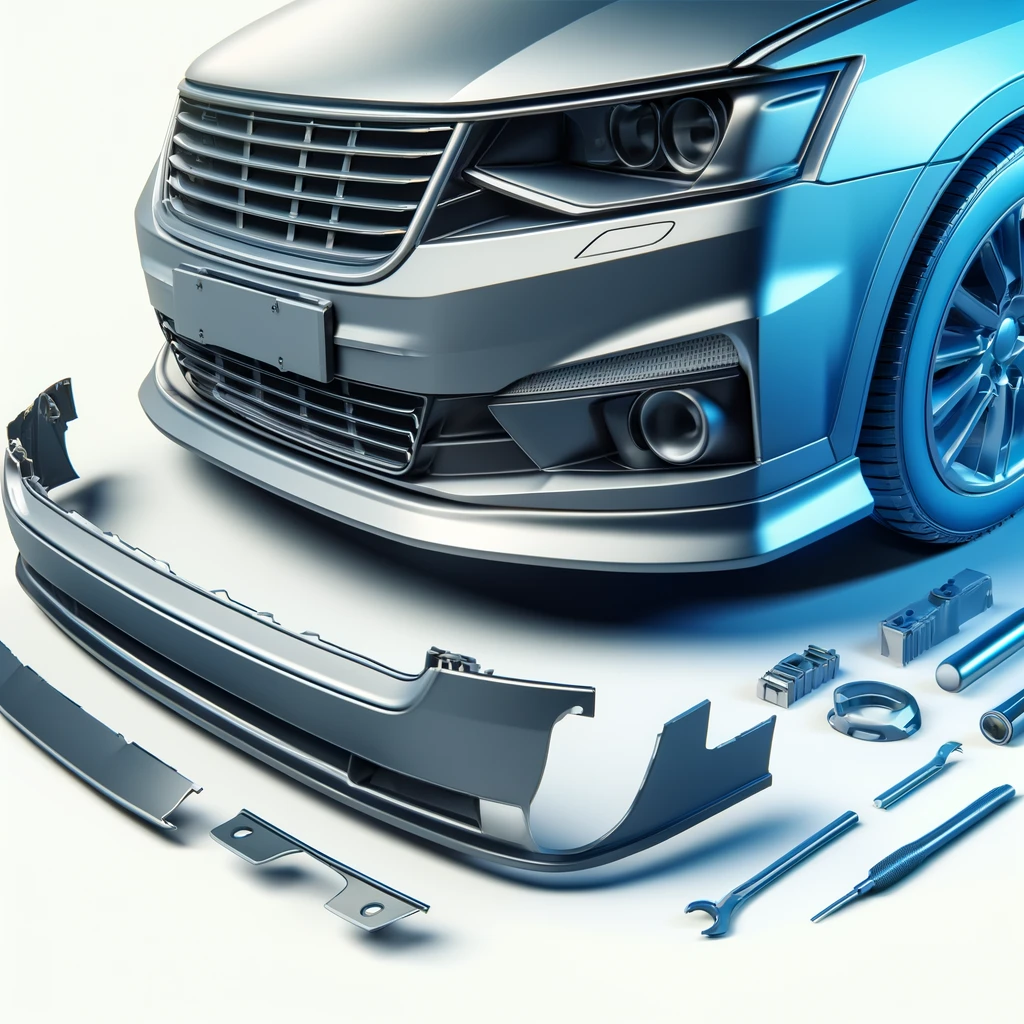
真空成形で作られる製品
真空成形で作られる製品には以下のようなものがあります。
- パネル
- カバー
- トレイ
- 家電製品の外装
- 自動車のパネル
- 医療機器のケース
圧空成形で作られる製品
圧空成形で作られる製品には以下のようなものがあります。
- 高精度が求められるカバー
- ディスプレイ部品
- 精密機器の外装
Point :真空成形と圧空成形の選択は、製品の精度やコストに大きく影響します。真空成形は大規模で低コストな製品に向いており、圧空成形は高精度が求められる製品に最適です。
真空成形・圧空成形の実践ガイド
成形における材料選定
真空成形・圧空成形で使用される材料の特徴
各材料の特徴を以下に示します。
- ABS: 強度と耐衝撃性に優れています。家電製品や自動車部品に使用されます。
- PVC: 耐薬品性があり、医療機器や化学装置に使用されます。
- PET: 透明性が高く、食品包装や飲料容器に使用されます。
- PC: 耐熱性と耐衝撃性に優れ、電子機器や防護具に使用されます。
型の材料の選び方
型の材料は、コスト、製品の精度、耐久性を考慮して選びます。以下は、各型材料の特徴です。
- 木型: 低コスト、プロトタイプや小ロット生産に適していますが、耐久性に欠けます。
- 樹脂型: 中程度のコストで、中ロットの生産に適しています。耐久性は木型よりも高いです。
- 金属型: 高コストですが、耐久性が非常に高く、大ロットの生産に適しています。
成形の工程とコスト
真空成形の加工例
真空成形で作られる製品の例は以下の通りです。
- 家電カバー: テレビや冷蔵庫の外装カバー。
- 車両部品: 自動車のダッシュボードや内装パネル。
- 医療機器パーツ: 医療機器のケースや部品。
圧空成形の加工例
圧空成形で作られる製品の例は以下の通りです。
- 精密機器の外装: 高精度が求められる電子機器の外装。
- デザインモデル: 複雑な形状を持つ展示用モデル。
真空成形・圧空成形のコストダウンのポイント
コストダウンのポイントは以下の通りです。
- 型の工夫: 簡単な構造の型を使用することでコストを抑える。
- 材料の選定: コストパフォーマンスの良い材料を選ぶ。
- 工程の効率化: 生産ラインの効率化によりコストを削減する。
成形時の注意点
成形におけるよくある質問と回答
以下は、成形におけるよくある質問とその回答です。
- 透明な材料の選定方法は?: PETやPCなどの透明性の高い材料を選びます。
- 少量生産時のコストは?: 型のコストを抑えることで少量生産でもコストを抑えることが可能です。
失敗しない設計のTips
成功する設計のポイントは以下の通りです。
- 抜き勾配: 成形品の取り出しやすさを考慮して抜き勾配を設計に取り入れる。
- 素材の厚み: 厚みの均一性を確保することで製品の品質を向上させる。
真空成形・圧空成形の失敗事例と対策
典型的な失敗事例とその対策方法は以下の通りです。
- シートのたるみ: シートの温度管理を徹底することで防止。
- 寸法のばらつき: 冷却時間を適切に設定することで寸法のばらつきを防ぐ。
Point :真空成形や圧空成形の成功は、適切な材料選定と型の選び方、そして細部への注意が鍵です。コストダウンの工夫も重要な要素です。
真空成形・圧空成形の最新技術と事例
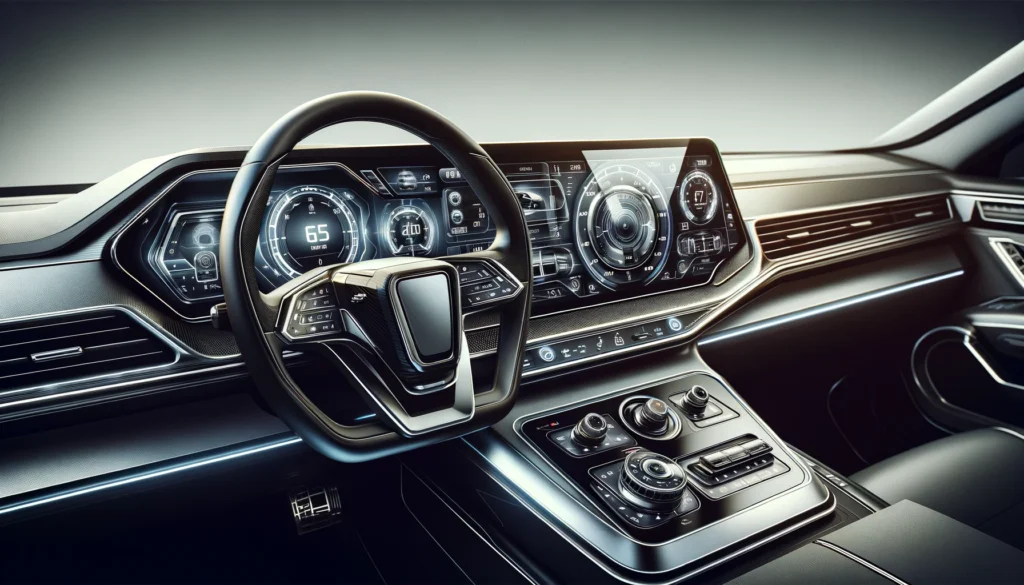
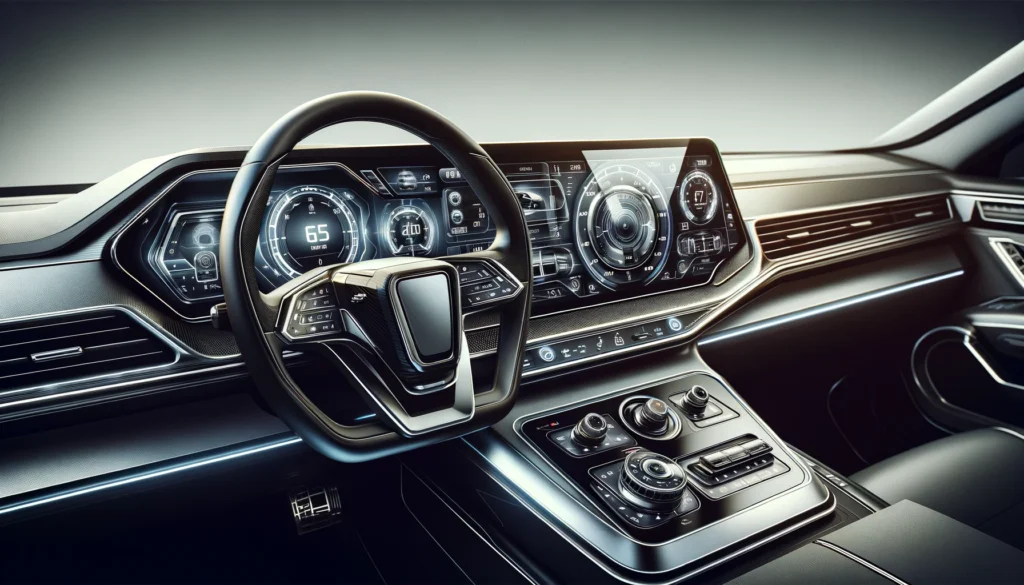
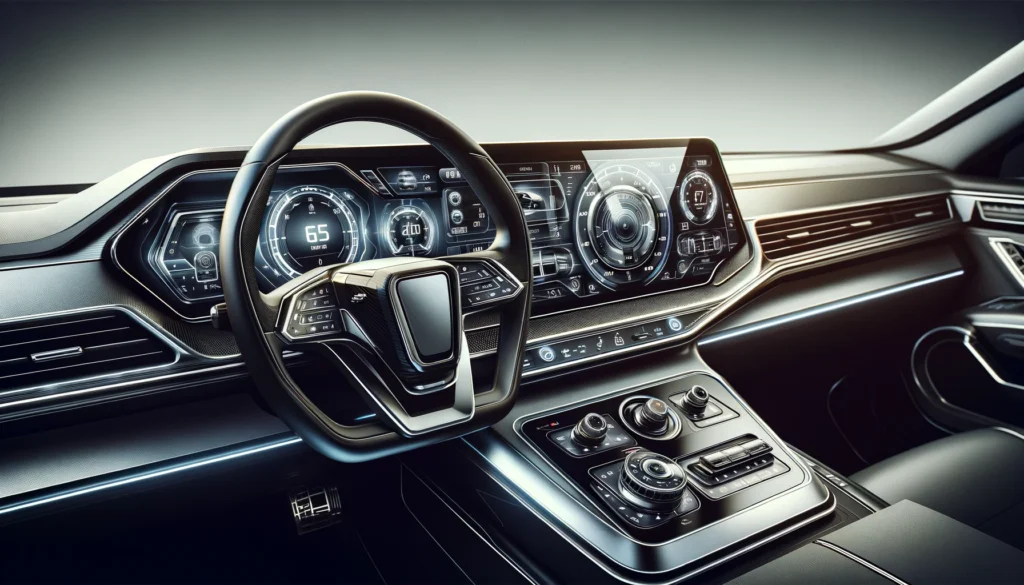
技術提案事例
真空成形に関する技術提案事例
3Dプリンティングを活用した型の作製や、高性能な真空ポンプの導入などがあります。
圧空成形に関する技術提案事例
温度制御の精度向上や、材料の均一な加熱技術などがあります。
成形品の事例紹介
真空成形の製品事例
以下は、真空成形の製品事例です。
- 家電製品: テレビの外装カバーや冷蔵庫の内装部品。
- 医療機器: 医療用トレイや器具カバー。
- 車両部品: ダッシュボードやインパネ。
圧空成形の製品事例
以下は、圧空成形の製品事例です。
- デザイン性が高い製品: 高級時計のディスプレイケースやデザインモデル。
- 精密機器の外装: 高精度が求められる電子機器の外装カバー。
Point :成形方法の進化はその可能性を理解する上で非常に役立ちます。具体的な事例を知ることで、自社の製品開発に役立てることができます。
真空成形・圧空成形の未来
今後の展望と課題
真空成形・圧空成形の未来予測
より高精度で低コストな成形技術の開発や、新材料の登場などが期待されます。
技術革新と新しい挑戦
バイオプラスチックの導入や、ナノテクノロジーを活用した成形技術などがあります。
環境への配慮
エコフレンドリーな成形技術
再生プラスチックの使用や、エネルギー効率の高い加熱システムの導入などがあります。
真空成形・圧空成形の持続可能性
製品ライフサイクル全体での環境負荷を考慮した設計や、廃棄物の削減を目指す製造プロセスの導入などがあります。
Point :真空成形と圧空成形の未来は、技術革新と環境への配慮が鍵です。持続可能な方法での成形技術の進化が求められます。
【追記】真空成形の最新動向(2024.7 更新)
- ハロゲン成形機の導入:
従来の遠赤外線加熱に代わり、ハロゲンヒーターを使用することで、加熱スピードの短縮と20mmまでの厚板成形が可能になっています。 - 大型化と軽量化の傾向:
年々大きな成形品の需要が増加しており、小型から大型化へと進んでいます。同時に、重量カバーから軽量カバーへの移行も見られ、真空成形品は大型軽量カバーとしての用途を拡大しています。 - バイオプラスチックの活用:
PLAなどのバイオプラスチックを使用した真空成形品が増加しています。特に食品容器分野では、コーヒーカプセルやヨーグルトカップなど、多様な製品が実用化され市場に流通しています。 - CO2超臨界成形技術の開発:
日本では、PLAの射出成形における「CO2超臨界成形」技術が開発されました。この技術は、溶融したPLAに超臨界状態の二酸化炭素を瞬時に溶解させて金型に射出する方法で、従来難しかった肉厚で強度のある成形品の製造を可能にしています。 - IoT化と生産システムの進化:
成形システム全体のIoT化が進んでおり、射出成形機を中心に、超臨界機装置、乾燥・材料供給システム、金型温度管理システム、ホットランナーなどの情報共有や制御が可能になっています。これにより、より効率的で高品質な生産が実現しています。
これらの動向は、真空成形技術の進化と応用範囲の拡大を示しており、特に環境配慮型材料の使用や大型・軽量製品の需要増加、生産プロセスの高度化が注目されています。
参考
成形の最新技術があれば教えて下さい。 | 真空成形・圧空成形.com (plastic-sheetforming.com)
参考
世界最高のPLA成形技術は日本にあり、加工に挑むユーザー急募 | 日経クロステック(xTECH) (nikkei.com)